This article is brought to you by Franklin Electric.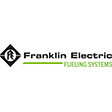
In today’s competitive convenience store market, operators are balancing more than just fuel sales—they’re managing customer expectations. When systems go down, operators don’t just lose sales, they can potentially lose customers, who may decide to take their business elsewhere, noted John Sevilla, global product manager at Franklin Electric. “Not only does every minute of downtime impact the bottom line, but also the customer experience of convenience, speed, and reliability.”
Fueling operations are complex, involving various interconnected systems that must work seamlessly. From pumps to price signage, even a minor outage can cause significant disruption, Sevilla explained. For instance, when a gas station's price sign goes down, it can confuse customers who may assume the station is closed.
In many cases, resolving such issues requires an expensive technician visit just to reboot the system and clear the issue—sort of like IT having you restart your computer. “As labor and service expenses rise, operators are increasingly adopting remote monitoring and control technologies to execute these types of reboots, reducing costs and improving efficiency. With the ability to act in real time, operators can ensure their customers aren’t left waiting for service, preserving the positive experience that keeps them coming back,” said Sevilla.
He continued, “That same store with a malfunctioning price sign can trigger a system reset using remote sequencing, which often clears the error and restores functionality without the need for a technician to visit the site and perform the same task.”
By acting quickly, operators can minimize downtime, avoid unnecessary technician visits, and improve the customer experience—saving both time and money, Sevilla noted.
This shift toward remote monitoring and control solutions is a win-win for operators. It not only reduces maintenance costs but helps maintain customer loyalty by minimizing disruptions in service. “Franklin Electric’s Remote Control Solution (RCS) empowers operators to take control of their fuel systems, managing outages quickly and efficiently from anywhere, without having to rely on technicians. Fewer truck rolls mean lower costs, and more uptime means happier customers,” said Sevilla.
“In a business where every interaction counts, reducing downtime and ensuring operational continuity is critical,” explained Sevilla. “Remote control technology is a powerful tool that keeps your site running smoothly, giving you the control you need to deliver the experience your customers expect.”
See the RCS in action and learn more with Franklin Electric’s Site Simulator.