This article is brought to you by Franklin Electric.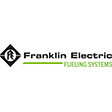
Managing both fuel systems and in-store operations has become increasingly complex, with operators needing to oversee not only fuel monitoring but also tasks like controlling cooler temperatures, managing lighting, and ensuring inventory levels are optimized.
According to Bill Gockman, senior global product manager at Franklin Electric, these responsibilities are not just operational necessities—they are critical for maintaining smooth business operations and customer satisfaction: “But as these tasks pile up, so does the demand on operators’ time and resources,” he said.
“On top of these day-to-day pressures, rising operational costs add to the strain,” Gockman said. “Each piece of equipment that malfunctions could result in revenue loss, as well as the expense of bringing a technician to the site. The key to overcoming these challenges lies in having a system, like Franklin Electric’s EVO™ Series, that doesn’t just monitor fuel but expands control across the entire location, automating essential processes and reducing the risk of costly issues before they escalate.”
Gockman said that “with the EVO™ Series, operators can leverage must-have site technology, like an automatic tank gauge (ATG), to do more than just fuel inventory and compliance monitoring to help operators optimize staffing and reduce maintenance costs.” He noted that operators are using the EVO™ to do various tasks such as automate lighting, monitor cooler temperatures, detect fuel thefts, identify corrosion, and more. When paired with other equipment, the EVO™ can also help detect and resolve outages in things like price signs, fuel dispensers, and other site controllers without a service call.
“This integrated approach gives c-store operators greater control over the entire site without increasing the workload, allowing employees to focus on customers,” he said. “By centralizing tasks, operators can enhance efficiency, stay ahead of potential issues, and create a more proactive operational environment.” Consolidating these functions reduces the need for multiple systems, minimizes service calls, and frees up time to improve the customer experience, Gockman added.
By bringing all key operational tasks into one comprehensive system, Franklin Electric’s EVO™ Series provides operators with the tools they need to reduce costs, simplify operations, and, most importantly, ensure a seamless experience for their customers by staying ahead of potential issues and keeping their sites running smoothly, Gockman noted.
Visit Franklin Electric at the PEI Show at NACS in Las Vegas, Booth #C6603, to learn more.